気候変動への対応
ヤマザキパングループのCO2排出量実績とエネルギー使用量実績
当社グループは、気候変動の緩和に貢献するため、工場、物流、小売店舗のそれぞれにおいて、CO2排出量削減対策に積極 的に取り組んでいます。2023年のScope1・2のCO2排出量は674千トン(前年比99.8%)でした。
-
CO2排出量
-
エネルギー使用量
算定範囲
山崎製パン株式会社、株式会社不二家、株式会社サンデリカ、ヤマザキビスケット株式会社、株式会社ヴィ・ド・フランス、株式会社東ハト、 株式会社ヤマザキ物流、株式会社サンロジスティックス、株式会社YKベーキングカンパニー(2022年以降に含む)の9社。ヤマザキパングルー プの連結売上高の9割に達します。ヤマザキパングループのCO2排出量の内訳(Scope1・2の実績)
当社グループの事業別(工場・事業所、物流、小売店舗)CO2排出量の2023年の内訳は、工場・事業所が521千tCO2(前年比100.1%)、物流89千tCO2(前年比101.0%)、小売店舗65千tCO2(前年比96.1%)で、構成比は工場・事業所が77%、物流が13%、小売店舗が10%でした。
-
① 工場・事業所
-
② 物流
-
③ 小売店舗
-
CO2排出量の内訳
工場・事業所における取り組み
エネルギー効率のよいシステム活用
工場で使用する電気エネルギーと蒸気や温水などの熱エネルギーを同時に効率よく供給するため、都市ガスを利用したコージェネレーションシステムを9工場に導入しています。コージェネレーションシステムは、発電された電気と発電時に発生した熱の両方を使用することで一次エネルギーの約70%以上が有効に利用できるため省エネルギーにつながり、CO2排出量の削減に寄与しています。9工場のコージェネレーションシステムにより、導入前と比べCO2排出量を年間で7,200トン削減しています。
また、導入している9工場のコージェネレーションシステムは、災害などの非常時に自立運転ができる仕様になっています。大規模停電が発生した際でも、ガスが供給されていれば電力の供給を行える機能を持っており、工場の稼働を継続させることができます。
さらに松戸第二工場と新潟工場への導入を予定しており、2025年の稼働を目指し計画を進めています。
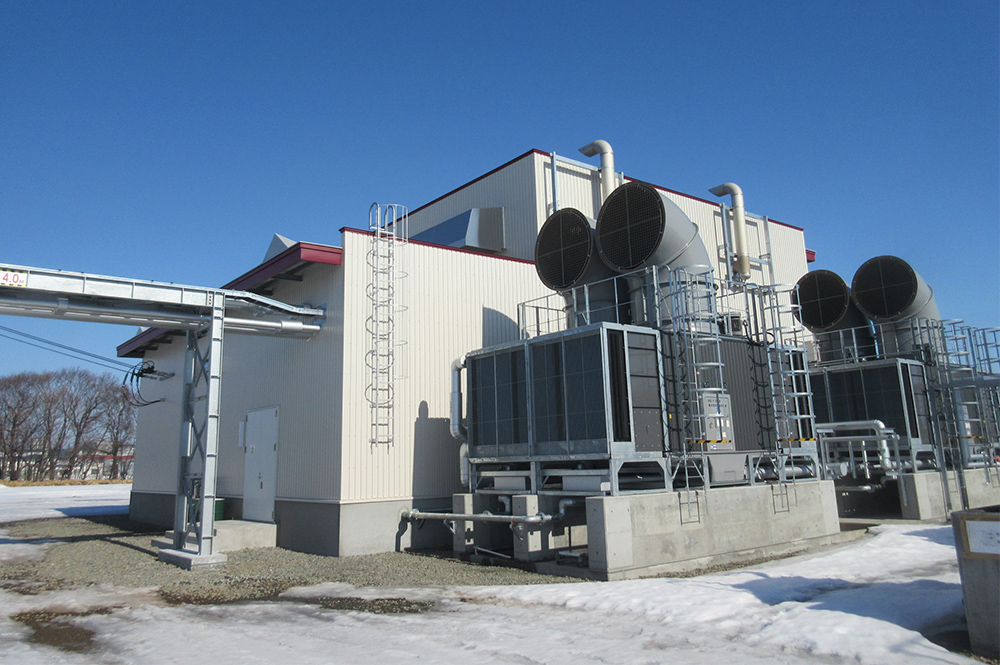
コージェネレーション設備導入(札幌工場)
省エネルギー機器の導入
LED照明の導入
各工場では省エネルギー推進の一環として照明のLED化を進めています。2023年はLED照明への交換を6,000台実施しました。これにより、CO2排出量を約360トン削減しました。
洗浄機の熱交換器
各工場の天板(パンなどをオーブンで焼くときにのせる鉄板)洗浄機や神戸工場の番ばんじゅう重洗浄機では使用する温水の熱(約60℃)を回収し、再利用しています。洗浄機に熱交換器を設置して排水された温水から熱を回収し、洗浄機の給水を加温することでエネルギー使用量とCO2排出量を削減しています。
伊勢崎工場ではバット(原料を保管しておくケース)洗浄機の排水された温水から熱を回収し洗浄機の給水を加温する熱交換装置を設置しています。
熱回収式電動コンプレッサー
各工場では、エネルギーの効率的な利用を目指し、ボイラーやコンプレッサーなどの設備を最新型の機器に更新しています。埼玉第一工場では、熱回収式電動コンプレッサーを導入し、圧縮空気をつくる過程で発生する熱を活用しています。これによりボイラーの給水を加熱しており、導入年に比べて年間でCO2排出量を約48トン削減しています。
再生可能エネルギーの活用
太陽光などの再生可能エネルギーを利用した発電設備を一部の工場で導入し、実効性の検証を行うとともに、従業員の意識高揚に役立てています。太陽光発電設備については、武蔵野工場、横浜第一工場、熊本工場、神戸冷生地事業所に小規模設備を導入しており、また古河工場では、2023年3月から、カーポート方式の太陽光発電設備(159.9kW)が稼働しています。2023年の発電量実績は、年間51,400kWhで、エネルギー使用量とCO2排出量の削減に貢献しています。
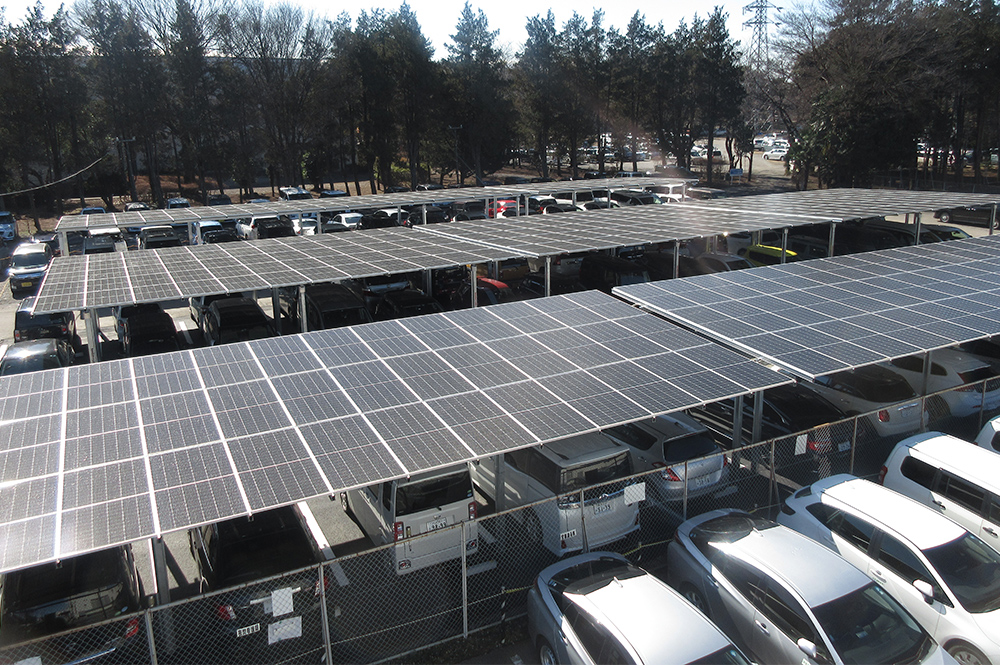
カーポート式太陽光発電設備(古河工場)
天然ガスへの燃料転換
当社は、重油やLPGからCO2排出の少ない天然ガス(都市ガス)への燃料転換を進めてきました。2008年から都市ガスのパイプライン未整備地域における「LNGサテライト方式」を利用した天然ガスへの燃料転換を進め、広島工場では2018年にLNGサテライト設備の設置とボイラー設備の更新を実施、2019年には各生産設備のオーブン燃料機器の燃料転換工事が完了しました。仙台工場では2020年11月から、十和田工場では2022年12月から、パイプラインによる都市ガス供給がスタートし、ボイラー設備の更新と各生産設備のオーブン燃料機器の燃料転換工事が完了しました。
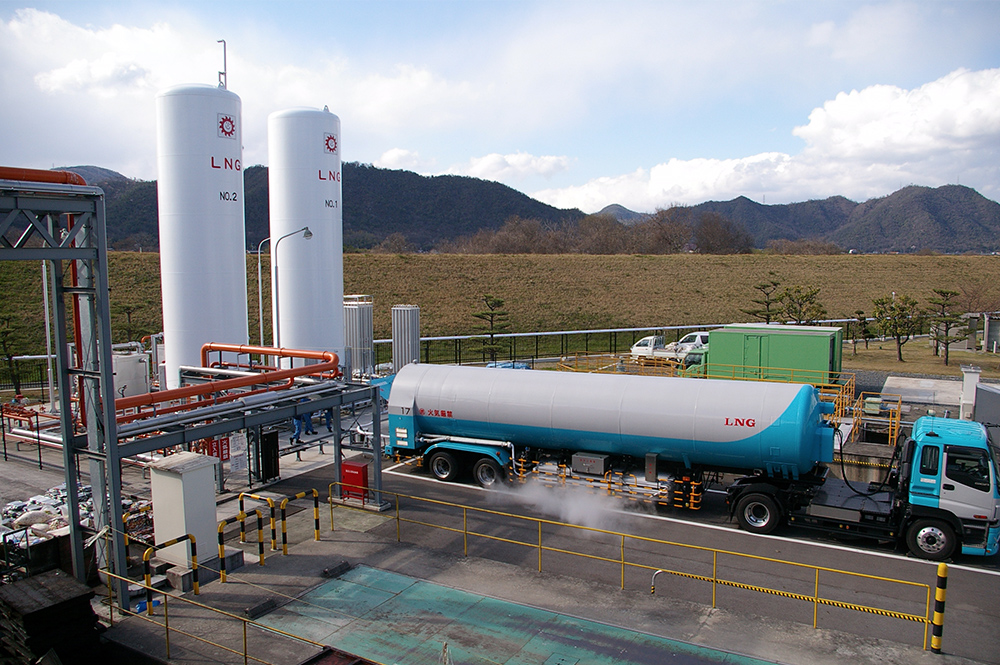
LNGサテライト設備(岡山工場)
フロン使用機器の管理
フロンは無色、無臭、不燃性で冷媒として優れた特性がありますが、地球温暖化係数がCO2の数千倍ある物質です。
当社では、工場の空調設備や冷却機器をはじめとして、店舗のショーケース、自動販売機や配送トラックの荷室の冷凍機などに、フロンを冷媒として使用しています。フロン排出抑制法改正により、企業への管理責務が一層強く求められている中、当社では法で定められている機器の簡易点検(出力7.5kW以上の機器は自社の有資格者による定期点検を実施)および修理時や廃棄時の管理ルールを定め、機器を適切に管理してフロン漏えいの抑制に努めています。
また、空調機器などの冷媒使用設備の新規導入や更新時は、地球温暖化係数の低い冷媒を積極的に採用するよう計画しています。2023年12月には、安城冷生地事業所の自動立体倉庫用冷却設備にCO2冷媒を使用した冷凍機を導入しています。
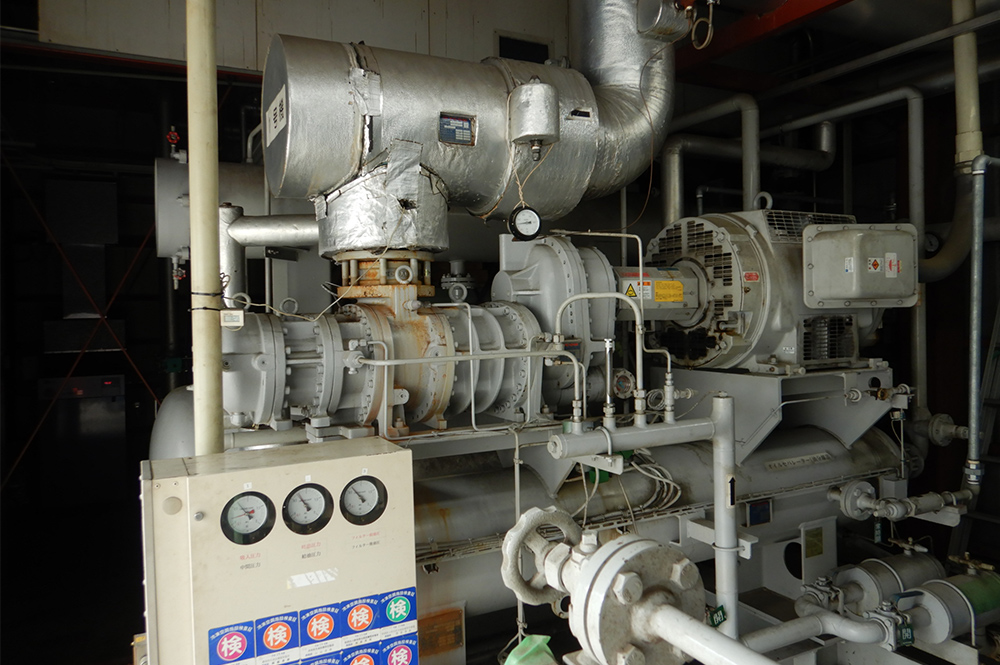
フリーザー用大型冷凍機(伊勢崎工場)
音響カメラを使用したエアー漏れ点検
当社の工場では、例えばパンの焼成時に使用する天板を移動させるためなどの機械のエアーシリンダーや、清掃時に使用するエアーガンにエアーを供給するために、コンプレッサーから配管やチューブを通して、各生産ラインにエアーを送っています。コンプレッサーの電気エネルギー使用割合は、工場全体の約1割を占めており、各工場では、エネルギーの効率的な使用を図るため、本社と連携し音響カメラを使用したエアー漏れ点検を行っています。この点検は、工場内の設備の中でエアー漏れ箇所から発する超音波を特殊なカメラで検知し、漏れ箇所を特定します。こうした点検方法を導入してから、人の五感による通常の点検では発見が困難な箇所のエアー漏れも補修することが可能となりました。エアー漏れが改善されるとコンプレッサーの負荷が軽減されるため、コンプレッサーを動かす電力の削減につながります。
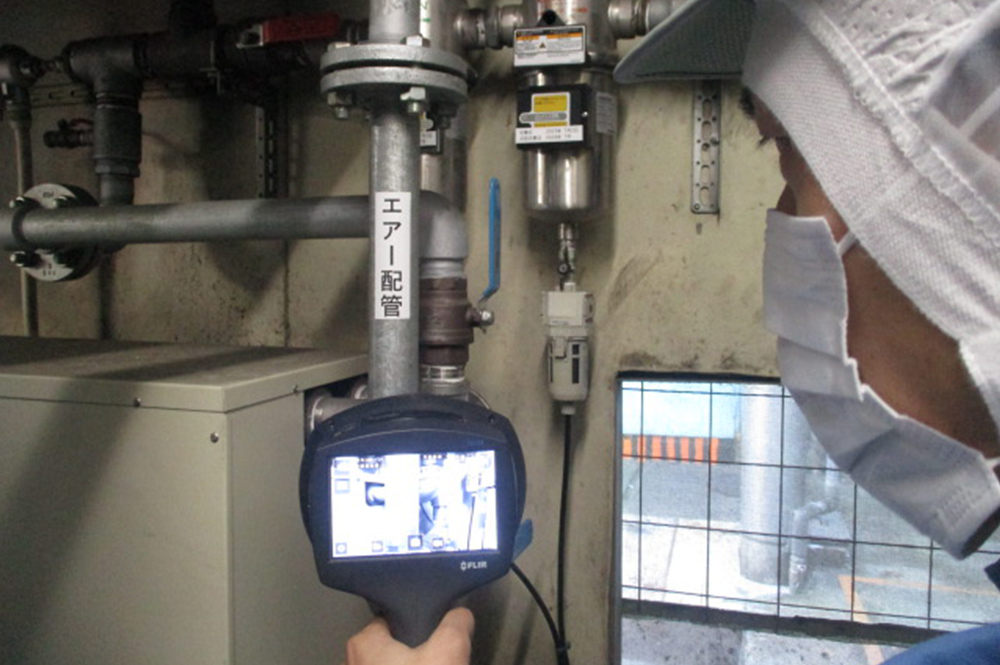
音響カメラを使用したエアー漏れ点検の様子
物流における取り組み
当社は、毎日、新鮮なおいしさをお客様にお届けするために、工場から販売店様へ直接配送する自社物流システムを採用しています。この物流システムにデジタル技術を積極的に導入し、GPSやドライブレコーダーと連動した配送管理による配送効率の向上とエコドライブ推進によるCO2排出量の削減を図っています。また、「デイリーヤマザキ」の物流を自社物流システムに取り込み、配送を合理化することにより、環境負荷の低減につなげています。
エコドライブの推進
2000年6月以降に配送部門を持つ全国20工場でエコドライブを実施する体制を整備し、2020年にすべての配送拠点に「車載端末」を導入しました。車両位置や運転状況をリアルタイムで把握できるようになり、配送中の急発進や急ブレーキの抑制を進めるなど、エコドライブを推進しています。当社では全国で1日当たり約2,700台のトラックが走っており、1日の走行距離は約317,000km(地球を約7.9周)です。軽油の使用量は2013年当時と比較して年間約1,600kℓ削減され、CO2排出量は年間約3,000トン削減されています。
運行管理システムによる走行距離の最適化
当社では「配送コース最適化システム」により、最適な配送ルートの構築を進めています。また、物量に応じて配送回数の集約(2回から1回へ)を進め、配送コースは5年前と比べて約100コースを集約しました。また店舗への到着時間や荷室の温度のほか、平均速度や急激な速度変化の回数などを車載端末に記録し、エコドライブに役立てています。
「デイリーヤマザキ」の物流自社化によるCO2排出量の削減
「デイリーヤマザキ」の店舗への納品は、外部の配送業者のトラックで届けられていましたが、2015年からチルド商品(牛乳・サンドイッチ・弁当)や冷凍食品(アイスなど)、2016年からドライ商品(食品・菓子・雑貨)の一部をパンと一緒の自社便で配送しています。この取り組みによって、店舗に納品するトラックの台数が削減され、CO2排出量削減につながっています。
「デイリーヤマザキ」の自社物流体制
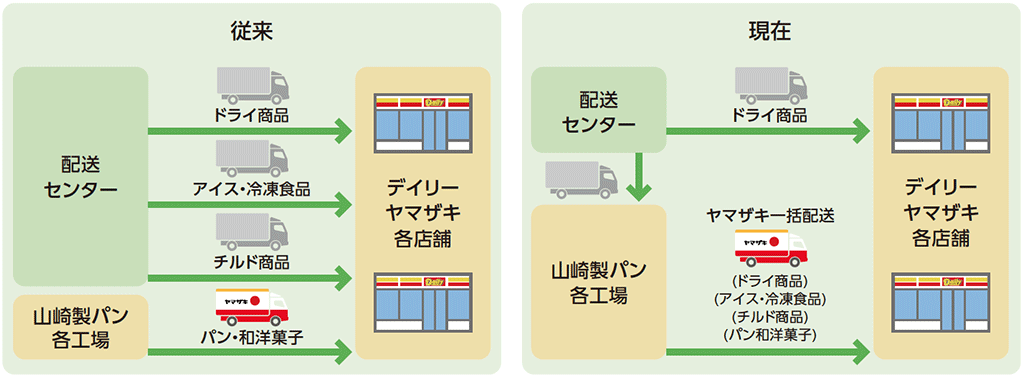
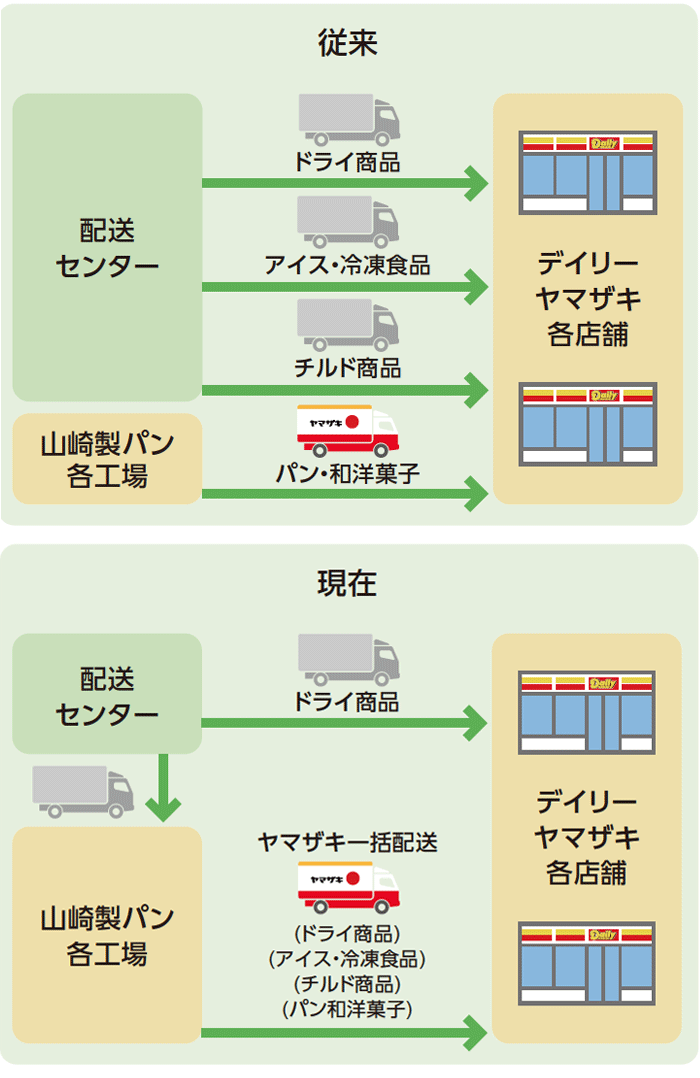
電気トラック(EV)の共同実験
2019年9月からCO2排出量の削減や騒音防止、大気汚染の防止に効果のあるEVトラックを導入して配送業務の実証実験を実施しました(2023年3月で実証実験終了)。いすゞ自動車様製のエルフEVトラックにチルド室を架装し、横浜第二工場において1日2便のルート配送を行いました。ディーゼルトラックと遜色ない使い勝手やCO2の削減効果を確認できており、今後導入に向けた検討を進めていきます。
モーダルシフト(鉄道輸送)の活用
一般的に鉄道輸送のCO2排出量はトラック輸送の12分の1といわれています。松戸第一工場ではCO2排出量の少ない貨物列車を活用した拠点間物流の運用を行っています。週3回の頻度でロングライフの製品を鉄道コンテナに積み込み南千住駅にて積み替え、札幌駅を経由して札幌工場に輸送しています。今後も引き続きCO2排出量の少ない輸送手段として、貨物列車の活用を検討していきます。
小売店舗からのCO2排出量削減の取り組み
「デイリーヤマザキ」では、省エネ機器の導入と店舗運営の工夫によって、エネルギー使用量の削減に取り組んでいます。店舗では、日々、機器の温度管理やフィルター清掃などの省エネ活動に取り組み、CO2排出量の削減を図っています。また本部においては、各店の電気・ガスの使用量等を集計し、エネルギー使用実績や利用状況等のデータを毎月店舗にフィードバックすることで、店舗と本部が協力してエネルギー使用量の削減に取り組んでいます。
「デイリーヤマザキ」店舗からのCO2排出量と
CO2排出量原単位の推移
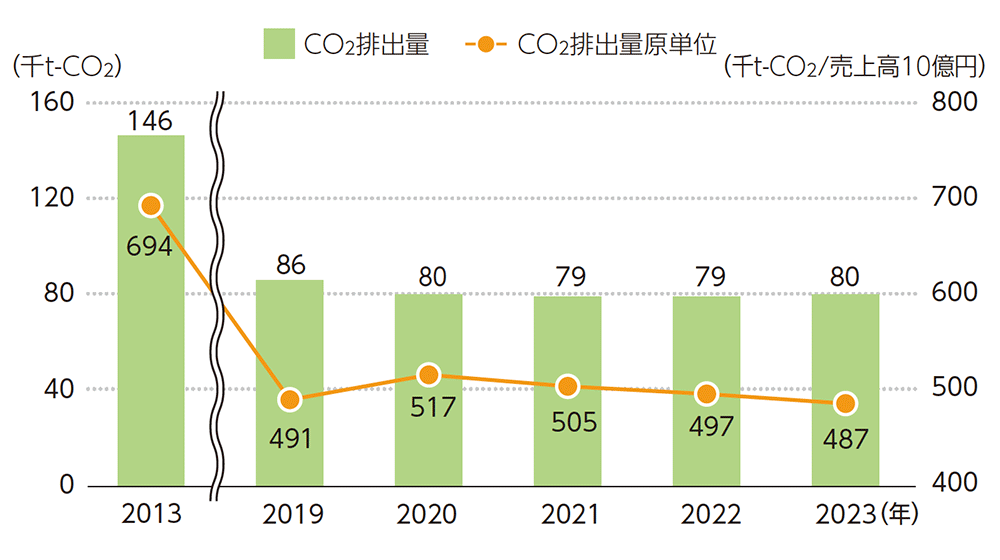
照明機器のLED化
照明は店舗の電力使用量の約30%を占めています。使用電力を少しでも減らす取り組みの一つが蛍光灯と比較して消費電力の少ないLED照明の使用です。「デイリーヤマザキ」ではLED照明を店内照明、看板照明およびパン棚照明に使用しています。また看板の照明には点灯・消灯タイマーを設置しており、電力使用量の削減に効果を上げています。
冷凍冷蔵機器の省エネ化
空調機器と冷凍冷蔵機器には高効率なインバータ仕様の機器を設置してエネルギー使用量の削減を図っています。一部の店舗では冷媒にCO2を使ったノンフロンの冷蔵ショーケース、冷蔵ウォークインケース、冷凍リーチインを設置して省エネ化を進めるとともに、地球温暖化に影響が大きいフロンの漏えい抑制にもつなげています。ノンフロン機器の導入は今後も拡大していく計画です。また、自社で保有する飲料自動販売機については、ノンフロン機器への入れ替えを進めており、約2,200台のうち約90%がノンフロン機器となっています。